Early screw jacks resembled bottle jacks in their appearance; these early devices featured a vertical lifting ram attached to a cylindrical body with a neck.
These jacks are operated with a rotating screw that extends and retracts their ram, offering an energy efficient alternative for heavy load applications.
Origins
Screw jacks are mechanical devices used to lift and position loads. They can either be powered by electricity or manually driven; both options allow users to link several together for added lifting power.
A worm gear or bevel gear mounted to a lead screw provides power transmission. This may be accomplished using a C-face adapter, right angle gear reducer or by remotely connecting the actuator worm shaft to a motor through couplings and connecting shafts.
Screw jacks come equipped with different thread profiles depending on their use, such as Acme lead screws, square or buttress thread and ball screw thread.
Types
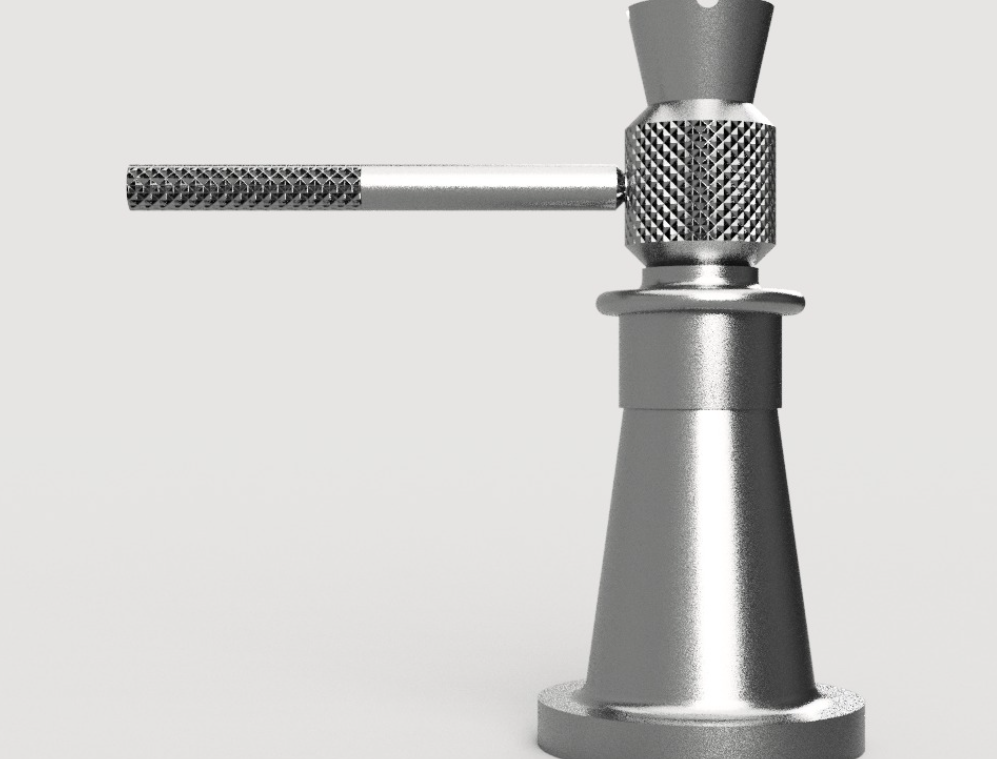
Screw jacks are manual or electric actuators used to move loads. Constructed of stainless steel, aluminum or other materials, screw jacks can be tailored for specific uses in various industries and environments.
This device includes a trapezoidal lifting screw, worm gear and worm wheel that rotate around its axis to move vertically up or down linearly, along with a flanged lifting nut that rides along its lead screw for reduced friction and wear on threads.
Bellows and limit switches can be added as optional accessories to further increase load capacity, safety, and operational efficiency.
Applications
Screw jack has many applications. Their primary use is lifting, lowering, pushing or pulling loads into position while holding them there securely.
Single, tandem and multiple jack systems can be configured into single, tandem and multiple jack systems and operated manually or using motors; manual operation may also be possible in some instances. When used to lift or position loads from kilograms up to thousands of tonnes they provide precise actuation, positioning or lifting solutions.
The type of jack system most suitable to you will depend on several factors, including load configuration and dimensions. Wide loads may necessitate more than two jacks to balance their load appropriately.
Design
Screw jacks are a form of gearbox assembly (worm gear or bevel gear) combined with an external transmission product such as lead screw, ball screw or roller screw to convert rotary motion to linear movement.
Design of screw jacks depends on their load configuration and dimensions, and may be installed individually or combined into “jack systems” featuring drive, connecting and safety components.
A screw jack’s capacity depends heavily on its duty cycle; higher duty cycles often necessitate larger models, lower input speeds or right angle reducers to meet power needs while remaining within its rated capacity.
Operating temperatures and environments can have a tremendous effect on how jacks operate, which is why Nook Industries offers a selection of jacks to meet these challenging environmental conditions.
Maintenance
Screw jacks are designed to raise vehicles for repairs and maintenance purposes. Their long handles allow users to turn clockwise until reaching their desired height, then counterclockwise when lowering.
These devices are exposed to daily wear and tear, so regular inspection and cleaning are necessary for their continued functionality.
Lubrication must also be conducted regularly on worm gear screw jacks that may operate in corrosive environments. This is especially essential.
Manufacturers advise that a hydraulic jack be checked and maintained every twelve months to prevent leakage or damage to its pump, cylinder, fittings, airside seals and oil side seals.